2023 / Q3 - Newsletter
- Theresa Hüpen
- Mar 2, 2024
- 5 min read
A lot has happened since the last newsletter: on June 2, we visited the MSC Osnabrück for a driver training session. We were able to test our new racing suits, which we would like to present to you in this newsletter.
We are also currently manufacturing a new monocoque, as not everything went perfectly in the first test. We would therefore like to tell you more about our monocoque and introduce two sponsors who are significantly involved in its production.

Dear sponsors, supporters and friends of Ignition Racing Team electric,
Today you receive the third newsletter of this season. A lot has happened since the last newsletter. On June 2nd we visited the MSC-Osnabrück for a driver training session. We were able to test our new racing suits, which we would like to present to you in this newsletter.
Three weeks ago, we carried out the summer cleaning that was urgently needed after our rollout with the support of LASCH Gebäudereinigung. We would like to express our special thanks for this, as our workshop was anything but clean and tidy until then. Freed from the sanding dust of the mono mold, we can now work in a clean environment again. After the work was done, we were able to fortify ourselves with a curried sausage stew cooked for us by the mother of our team colleague Nick Koldeweihe.
We would also like to thank all the sponsors who visited us in our workshop last Friday. During the meet & greet we organized with our sponsors, we were able to show them our workshop and the current state of our car. Afterwards, we ended the evening with a cozy barbecue.
We are currently manufacturing a new monocoque, as not everything went perfectly in the first test. We would therefore like to explain more about our monocoque in the rest of this newsletter and introduce two sponsors who are significantly involved in its production.
With racing greetings
Your Ignition Racing Team electric

The production of the monocoque is the task of the Chassis department and due to various adjustments to the vehicle concept, a completely new monocoque was designed, constructed and manufactured. The monocoque is made of carbon fiber with a foam core and is the connection point for all other components and thus also forms the passenger safety cell. For this reason, particular attention must be paid to compatibility with all other assemblies in the design.
Joris Rehsöft was responsible for developing the geometry and the laminate, which was completed as part of a semester project with Prof. Dr. Christian Schäfers, as this was combined as one construction site which is normally divided into four individual construction sites. All automotive engineering students at Osnabrück University of Applied Sciences have to complete a project of this kind as part of their studies and these are always a good opportunity to integrate the work of our team members into their studies.
The aim of the construction site was to optimize the weight of the chassis and improve its rigidity. In addition, it should be possible to position the connection points in the vehicle more precisely during the manufacturing process in order to simplify production. This is reflected, for example, in the particularly strong design of the chassis connection points.
What did the collaboration look like?
The production of the monocoque posed a number of challenges, but these were overcome in close cooperation with our two long-standing sponsors DD-Compound and Schäfer Modellbau.
Thanks to the tireless efforts of Schäfer Modellbaus, we were able to produce our monocoque mold (photo) for the first time in years exactly according to our requirements and the unusual effort required for the competition. Compared to the previous season, in which we had a 4-part monocoque mold, we now have a 12-part monocoque mold so that we can produce and demold our silhouettes.
During the subsequent production phase, Dominik Dierkes, founder and owner of DD-Compound, was always at our side. He answered our questions late into the night, even at unusual times, and also surprised us with visits to monitor and accelerate the progress of the project.
What has changed compared to the previous year?
Due to the concept change of the overall vehicle and detailed research and consultation with sponsors, we have already been able to save 23kg in the entire chassis assembly this season compared to last.
This season, we are building a one-piece monocoque using the infusion process for the first time. As we had no experience with this new production method, we are currently in the process of manufacturing our first upgrade part. Our aim is to reduce the weight by a further 20%.
We were also able to reduce the production process for the entire monocoque to four days instead of three to five weeks. This is mainly possible because the company DD-Compound has made its tempering furnace, in which Revolution Race Cars were previously treated with heat, available to us on permanent loan.

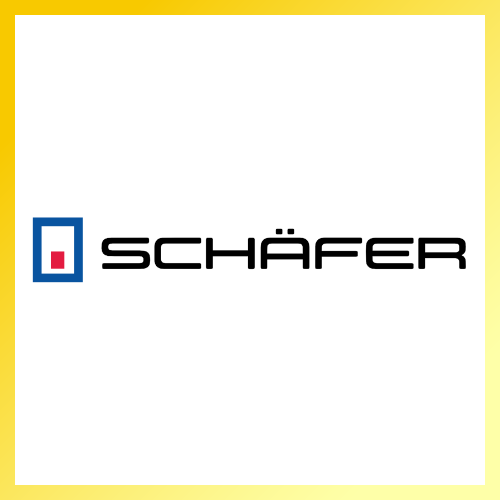
"Bringing design to life & creating emotions"
Schäfer Modellbau is an innovative company with 200 employees at its sites in Osnabrück and Mühlhausen (Thuringia). With a broadly diversified portfolio, the company presents itself as a full-service provider with a very high level of vertical integration for the automotive industry and other sectors.
In the automotive sector, the areas of project management, design, construction, product manufacturing and model making are covered. In addition, individual solutions are developed for a wide range of industries. With flexibility, know-how and a large machine park, Schäfer Modellbau has been developing solutions for customers for over 100 years.

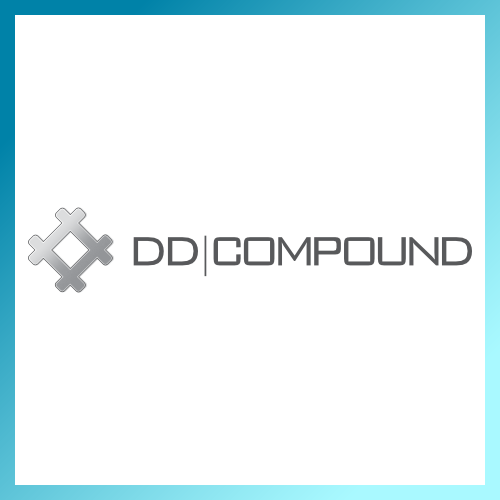
The company DD-Compound GmbH was founded over 14 years ago by Dominik Dierkes in Ibbenbüren and specializes in the development and production of auxiliary materials for vacuum infusion. The products simplify processes, make them safer and increase product quality.
This allows projects to be realized that would otherwise be exposed to a higher risk. DD-Compound has successfully established itself in the composites industry worldwide - from product applications in 100m rotor blades for wind turbines, shipbuilding and automotive to the smallest special components. As Dominik Dierkes himself was once a member of the Ignition Racing Team, DD-Compound is particularly keen to support Formula Student teams worldwide.

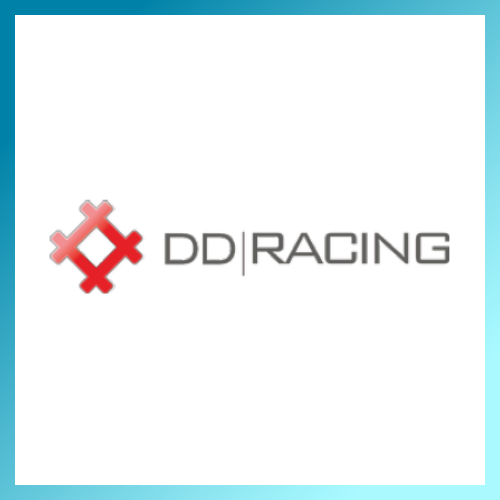
The company Dierkes Racing GmbH with the racing team DD-Racing is an up-and-coming motorsport team in Ibbenbüren, Westphalia, which has been active in prototype motorsport for almost 10 years. With the cooperation of the English racing car manufacturer Revolution Race Cars, the company looks after customers all over the world and takes part in many events in Europe. DD-Racing achieved its first successes in the Superlight Prototype Series in 2015.
The Dutch Supercar Challenge brought together many racing series in 2016, which brought a lot of attention to prototypes and the racing team. With the launch of the new Revolution A-One at the end of 2018, other series opened up, such as the Sports Prototype Cup. Since September 2022, the company has been supporting many customers in professional motorsport and, in addition to servicing, also offers the rental of racing vehicles.

A few weeks ago, our team received our racing suits for this season. Racing suits are essential to protect the rider from injuries and burns in the worst case scenario. That's why it's important to have completely intact equipment, which we ensure with the new suits.
We are particularly pleased about our racing suits this season, which are sponsored by Dierkes Racing and DD-Racing, because they have the color of our IR23 as an accent color and an embroidery with the logos of both Dierkes Racing and DD-Racing as well as the IRTe.
New racing suits are also planned for every season in the future - we look forward to working with you!

Commentaires